Pembuatan ramping membolehkan anda mengoptimumkan semua proses perniagaan dalam perusahaan. Ini bertujuan untuk menghilangkan kos, melancarkan proses pengeluaran berterusan, dengan fokus pada pengguna akhir.
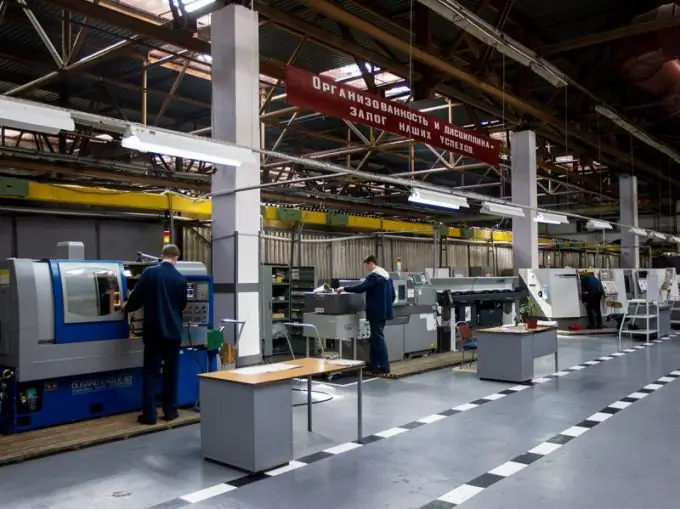
Prinsip ramping sering digunakan di perusahaan untuk mengurangkan kos. Dengan bantuan mereka, menjadi mungkin untuk mengurangkan jumlah tindakan yang tidak dapat menambah nilai pengguna dalam proses pengeluaran.
Pembuatan ramping merujuk kepada skim pengurusan khas untuk sebuah syarikat. Idea utamanya adalah berusaha untuk menghilangkan segala jenis kos, untuk memasukkan setiap pekerja dalam prosedur pengoptimuman. Skim sedemikian ditujukan sepenuhnya kepada pengguna.
Sejarah
Pengasas konsep tersebut adalah Taiichi Ohno, yang mengembangkan prinsip asas. Dia telah bekerja di Toyota Motor Co sejak tahun 1943. Pada tahun 1945, Jepun kalah perang, untuk bertahan dalam kemelesetan, diperlukan pendekatan baru untuk menyelesaikan masalah. Pada tahun-tahun itu, Amerika adalah pemimpin yang tidak dipertikaikan dalam industri automotif. Selama bertahun-tahun ia telah mengurangkan kos dengan meningkatkan pengeluaran besar-besaran. Gaya ini cepat berlaku di semua bidang.
Presiden Toyota Motor Co mengatakan bahawa perlu bersaing dengan Amerika dalam tiga tahun. Sekiranya ini tidak dilakukan, maka industri automotif di Jepun tidak akan bertahan. Oleh itu, semua usaha dihabiskan untuk mengembangkan sistem pengeluaran mereka sendiri, yang berbeza dengan sistem pengeluaran besar-besaran tradisional Jepun. Pada saat yang sama, tujuan tersebut dicapai bukan dengan memperluas wilayah produksi, tetapi dengan menghasilkan mobil dalam jumlah kecil sesuai dengan skema baru.
Faktor utamanya adalah bergantung pada faktor manusia dan mewujudkan suasana tolong menolong. Prinsip baru yang diperkenalkan diterapkan tidak hanya pada karyawan, tetapi juga untuk pelanggan dan pembekal. Selama 15 tahun akan datang, Jepun mengalami pertumbuhan ekonomi yang luar biasa pesat.
Ciri dan prinsip
Perkara utama adalah penilaian nilai produk pembuatan untuk pengguna tertentu. Situasi diciptakan di mana terdapat penghapusan kerugian yang berterusan. Ini memungkinkan untuk membuang tindakan yang memakan sumber, tetapi tidak membentuk nilai. Taiichi Ohno mengenal pasti beberapa jenis kerugian:
- kerana pengeluaran berlebihan;
- masa menunggu;
- pengangkutan yang tidak perlu;
- langkah pemprosesan yang tidak perlu;
- pembentukan stok berlebihan;
- pergerakan objek yang tidak perlu;
- berlakunya produk yang rosak.
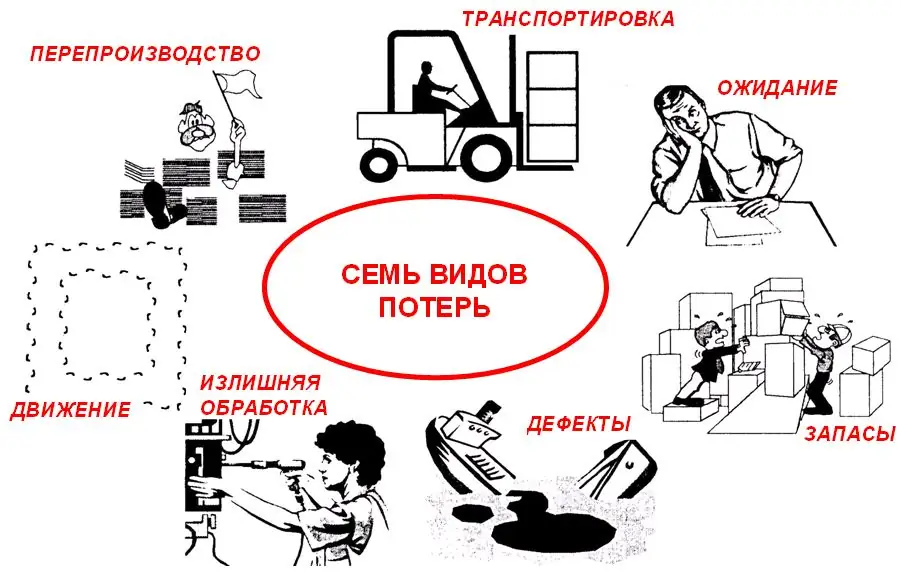
Merujuk kepada jenis kerugian dan prestasi operasi yang tidak rata. Ini berlaku, misalnya, dengan jadual kerja sesebuah syarikat kerana turun naik permintaan di pasaran pengguna.
Untuk melaksanakan pembuatan tanpa lemak, perlu bukan hanya untuk mengatasi kerugian, tetapi juga untuk menerapkan prinsip-prinsip asasnya. Yang pertama mengandaikan: anda perlu menentukan apa yang mencipta nilai produk dari sudut pandangan pengguna. Kadang-kadang sejumlah besar manipulasi dilakukan di perusahaan, yang ternyata tidak penting bagi calon pelanggan. Pendekatan ini akan membolehkan anda menentukan proses mana yang difokuskan untuk memberikan nilai dan mana yang tidak.
Prinsip kedua bertujuan untuk mengenal pasti perkara penting dalam keseluruhan rantaian pengeluaran dan menghilangkan sisa. Untuk ini, semua tindakan dijelaskan secara terperinci dari saat pesanan diterima, hingga pemindahan produk terus kepada pembeli. Ini membolehkan anda mengenal pasti apa yang diperlukan untuk mengoptimumkan kerja dan merangsang pengeluaran.
Prinsip ketiga melibatkan aktiviti penyusunan semula sehingga mereka mewakili aliran kerja. Aspek ini menganggap bahawa semua tindakan mesti dilakukan agar tidak ada waktu henti di antara mereka. Kadang kala aspek ini memerlukan pengenalan teknologi baru. Kemudian semua proses terdiri daripada tindakan yang memberi kesan positif terhadap produk itu sendiri.
Prinsip keempat adalah perlunya melakukan tindakan yang perlu bagi pengguna itu sendiri. Organisasi hanya boleh menghasilkan produk setakat yang mencukupi.
Prinsip kelima adalah perlunya peningkatan berterusan dengan mengurangkan tindakan yang tidak perlu. Melaksanakan sistem tidak akan berfungsi sekiranya prinsipnya hanya digunakan sekali-sekala. Sekiranya anda memutuskan untuk mula melaksanakan sistem, anda perlu melakukan ini secara berterusan.
Alat bersandar
Mereka mempermudah penggunaan prinsip kurus. Alat tersebut digunakan secara individu dan digabungkan. Ini termasuk:
- Organisasi ruang yang betul. Pemahaman masalah berlaku, pengesanan pelbagai penyimpangan.
- Sistem pelaporan masalah. Satu isyarat khas diberikan. Ia dibenarkan menghentikan pengeluaran untuk mengelakkan berlakunya kecacatan secara besar-besaran.
- Aliran penjajaran tanpa gangguan dan pengumpulan buffer. Alat ini memungkinkan untuk menghilangkan pelbagai jenis kerugian mulai dari lebihan stok.
- Perkara yang paling penting berlaku bukan di pejabat, tetapi di tempat pengeluaran. Penglibatan pihak pengurusan mengurangkan masa reaksi apabila timbul masalah. Disiplin dan maklumat langsung diperkukuhkan.
- Kecekapan keseluruhan peralatan sentiasa diperiksa. Alat ini mengesan tiga kategori kehilangan peralatan: ketersediaan, produktiviti, dan kualiti.
Terdapat alat pembuatan lain yang ramping, yang semuanya bertujuan untuk ketelusan proses pengurusan, mengurangkan kos kualiti produk dan meningkatkan penglibatan pekerja dalam proses pengeluaran.
Ciri Kaedah Pembuatan Lean
Konsepnya mudah difahami, tetapi sukar untuk menjadikannya berfungsi dalam praktik. Sering kali, melaksanakan prinsip memerlukan perubahan dalam keseluruhan budaya syarikat. Ini mungkin memerlukan bukan sahaja masa, tetapi juga wang. Konsep ini difokuskan pada pertimbangan maksimum kepentingan pelanggan dan pengguna. Pengaturan semua proses yang tinggi membolehkan anda mengelakkan kos yang tidak perlu dan bersaing di pasaran moden.
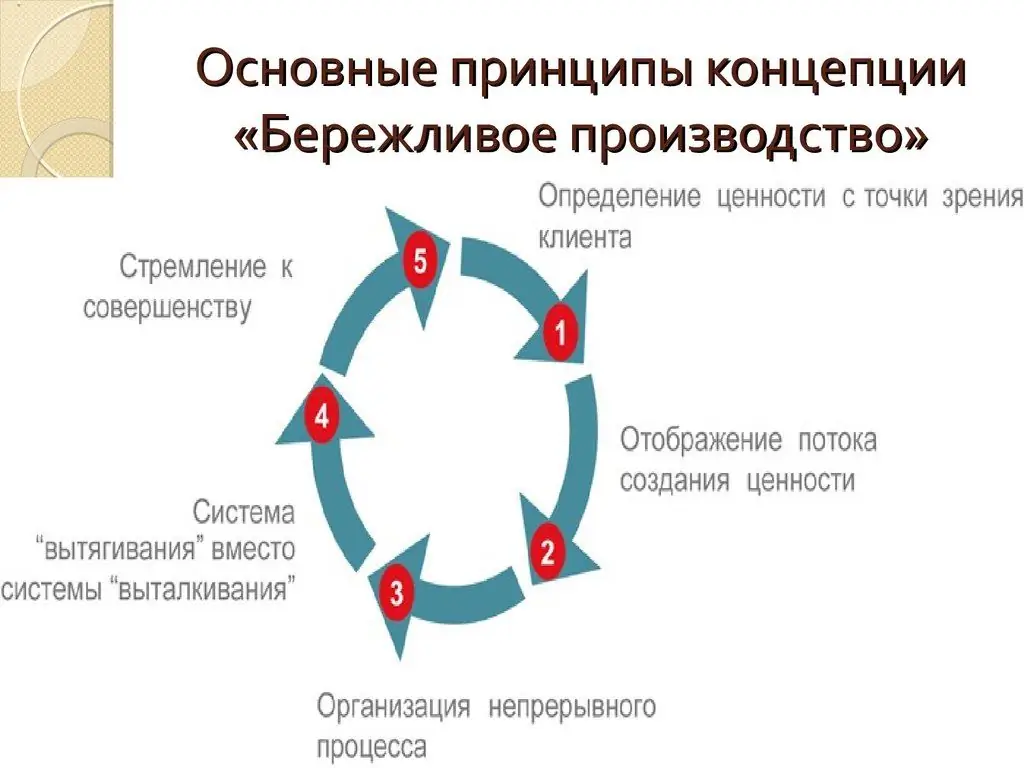
Pengalaman dunia menunjukkan bahawa pelaksanaan prinsip yang dijelaskan:
- meningkatkan produktiviti pekerja sebanyak 35-70%;
- mengurangkan masa kitaran pengeluaran sebanyak 25-90%;
- mengurangkan kemungkinan perkahwinan sebanyak 59-98%;
- meningkatkan kualiti produk sebanyak 40%.
Prinsip ramping dapat diterapkan di berbagai bidang. Aspek-aspek ini sangat relevan dalam pengeluaran, logistik, perbankan, perdagangan, penciptaan teknologi maklumat, pembinaan, dan perkhidmatan perubatan.
Pelaksanaan prinsip berlaku dalam tiga peringkat. Pertama, terdapat kajian mengenai permintaan. Untuk ini, pengiraan nada, waktu penggunaan dan teknologi khas lain digunakan. Pada peringkat kedua, kesinambungan aliran nilai tercapai. Beberapa langkah diambil yang memungkinkan untuk menyediakan produk dengan pengguna tepat pada waktunya dan dalam jumlah yang tepat. Pada peringkat ketiga, pelicinan berlaku apabila terdapat pengagihan isipadu dan kerja yang seimbang.
Pelaksanaan akan berjaya jika pelbagai alat dan sumber digunakan dalam proses tersebut, dan rancangan latihan dan kelayakan pekerja telah disetujui. Yang terakhir ini penting, kerana ketika bekerja di sebuah syarikat, orang biasanya diundang yang mempunyai pengetahuan, kemahiran dan pengalaman yang berbeza. Anda boleh belajar dari pengalaman menggunakan program latihan khas dan dengan memerhatikan rakan sekerja.
Di samping itu, Lean Manufacturing melibatkan pengembangan kreativiti dalam diri pekerja. Pendekatan ini membolehkan anda melangkaui perusahaan tertentu untuk bekerja dengan berkesan ke arah mana pun. Semua pekerja mesti dapat mencari penyelesaian yang berbeza untuk situasi yang sama.